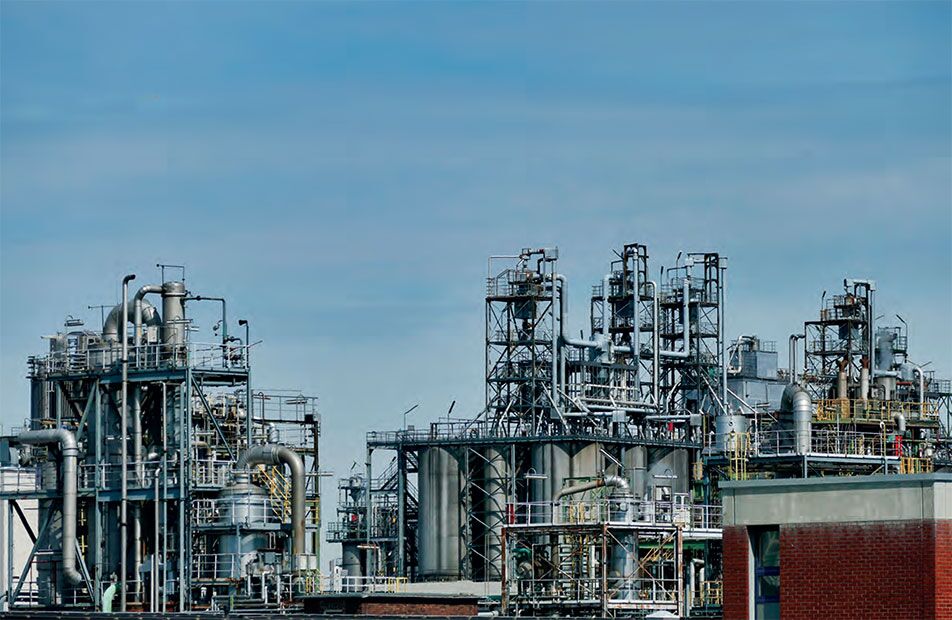
The essential prerequisites to provide added value solutions to clients are, on one hand, having the specific competence to understand the actual requirements being put forward, and on the other hand the presence of dedicated structures to be able to design and realize them. With this idea, Pneumax set up over the years a “specialization” process which led to a restructuring of the company’s organization involving the creation of vertical divisions, dedicated to segments characterized by highly specific technologies and applications: from industrial automation to the automotive industry, right up to process automation.
Created in 2016, the Process Automation division develops products and solutions dedicated to sectors which require specific materials, such as stainless steel in the Food&Beverage segment, or special performances such as working pressure in the Oil & Gas segment, one of the domains where Pneumax is focusing its investments. The company is now capable of manufacturing and selling a vast range of components which differ in terms of size, performance and materials used, selected according to the products used in the process: gas, oil and other chemical and petrol-chemical products.
Operating in these industries also implies ensuring compliance with international quality standards. Pneumax holds ISO 9001:2008, ISO 14001:2004, OHSAS 18001:2007 certifications as well as such product certifications as ATEX, EAC, FM, NEPSI and CU_TR012, and SIL (Safety Integrity Level) certifications relative to product performances in terms of reliability.
Pneumax follows the clients from pre-sale to technical service and maintenance following the delivery of the product.
A significant applicative case is represented by the pneumatic control systems for the actuation of On-Off valves, engineered and produced in Manifold configuration following Shell’s design specifications for the Deep-water Shell Vito oil rig, placed in the Gulf of Mexico, 240 Km South-West of the coast of New Orleans.
The manifold configuration of this solution brought about considerable advantages from an economic as well as technical standpoint. The solution suggested by Pneumax turned out to be competitive both in terms of floor space – a highly relevant aspect in Off-shore applications where available space is limited – and in assembly terms, thanks to the significant optimization of the use of pipe fittings needed to connect the various pneumatic operators assembled on the control system’s panel. Besides, being a NACE Off-shore application, all components used were made out of AISI316L stainless steel, a “noble” material which can guarantee reliability and durability over time. In terms of cost containment, the reduction of weight and of material consumptions was valued positively both by Limitorque Flowserve, Pneumax’s direct client, and by Shell, the project’s End User.
The capability of seeking innovative solutions, supported by organizational flexibility, the experience in design and the ability of project management in defining increasingly customized solutions today allows the Process Automation division of Pneumax to be acknowledged by the main international players, both EPC contractors and end users.